How can Bayer promote a continuous improvement approach through the management of its processes?
Bayer operates in a sector subject to strict normative constraints. To meet these requirements, the company wanted to implement an integrated QSE management system, based on a process-based management approach.
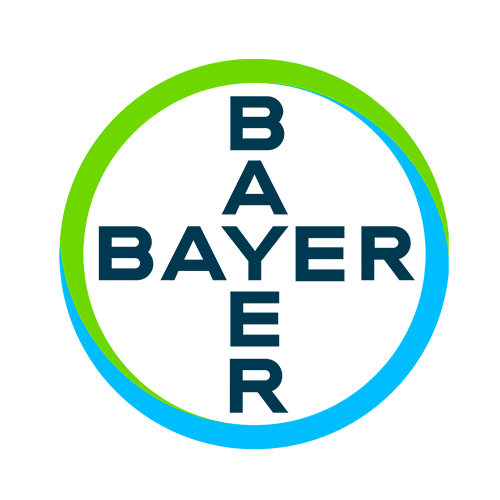
- Pharmaceuticals
- 3250 employees – 9 R&D sites and 7 production sites
- Lyon (69)
BAYER client case
Context
The Bayer Villefranche site is a Seveso 3 high threshold site. As a result, it must meet a large number of requirements and implement an effective policy for the prevention of major industrial risks
Thus, we regularly review our organisation in order to meet the challenges of safety and environmental protection, developing employee skills and initiative, improving the efficiency of production and support services, etc.
PYX4 is an easy-to-use solution, which has enabled us to meet very specific normative requirements, while allowing the entire system to be shared via a simple intranet browser.
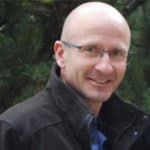
Thierry DESCHOMBECK
Continuous Improvement Manager
BAYER CROPSCIENCE
Pharmaceutical
The main stages of the project
Implementation of the PYX4 Process solution
Ensuring the safety of employees, local residents and installations
Ensuring the proper application of QSE procedures and standards
In brief
How to harmonise practices and implement common processes?
Objectives
- Determine a target organisation
- Formalise and share processes across 14 sites
Context
- 14 training centres
- Different practices
Results
- Structuring our process approach
- Trained and structured teams
- 28 PUs and 14 graphs already modelled
Solutions
Bayer uses the PYX4 Process & Improver modules
Discover the integrated solution at Bayer Cropscience and start a similar approach to meet your challenges and objectives.
Our teams are available to answer your questions.
Interview
Thierry DESCHOMBECK / Continuous Improvement Manager
How did you hear about our solution?
At the time of the CRFPs, the CRFP in Limoges was a satisfied user of Qualigram, a software suite that has evolved into PYX4, so we studied PYX4 among other solutions on the market.
What did you find relevant in our offer? What convinced you to choose PYX4?
The easy-to-understand modelling methodology and the tool’s accessibility to all via standard internet access were big advantages, as well as the simple operation and document management with the workflow principle.
The PYX4 Improver module, which enables the reporting of malfunctions in processes or procedures.
More generally, the modularity of the suite’s offer, which allows the software to be enriched with new functionalities as the internal approach matures.
We appreciated the possibility offered by the PYX4 tool to access and manage documents already existing on other storage spaces, such as operating procedures for example, directly from the procedures modelled in the tool.
Finally, the support offers around the implementation of a process approach, which were not proposed by the other editors consulted.
What are the expectations linked to this project and more generally to the Quality approach?
Our objective is to finalise the modelling of our processes within the next 6 months, and all our procedures within a year, before continuing with the modelling of work instructions in the format made available in PYX4.
How did you organise yourself to involve the project stakeholders?
We identified 14 macro-processes, representing the general mapping of our organisation. For each macro-process, we appointed a pilot responsible for modelling in PYX4 the process for which he or she is responsible, as well as all the related procedures. Each pilot is assisted by a modeller, and is of course supported, monitored and supervised by the project team of which I am a member.
PYX4 helped us to think about our process approach, to build our processes and procedures and to train our pilots and modellers in the tool itself.
PYX4 Customer Stories
Read our latest customer stories
We could tell a lot of stories about our products and services, but the voice of our customers is still the best. Discover their experiences and learn about the challenges they faced using the Pyx4 platform.