The 2017 edition of the Quality Barometer reveals a growing interest among organizations to implement an integrated management system (IMS) and thus, regardless of size or industry.
Companies are facing 2 major challenges. On the one hand, they are less and less tolerant of risks related to their activity such as quality or safety problems because this has a negative impact on customers and investors. On the other hand, companies want to rapidly develop their creative capital, their agility and their strategic performance to gain new competitive advantages.
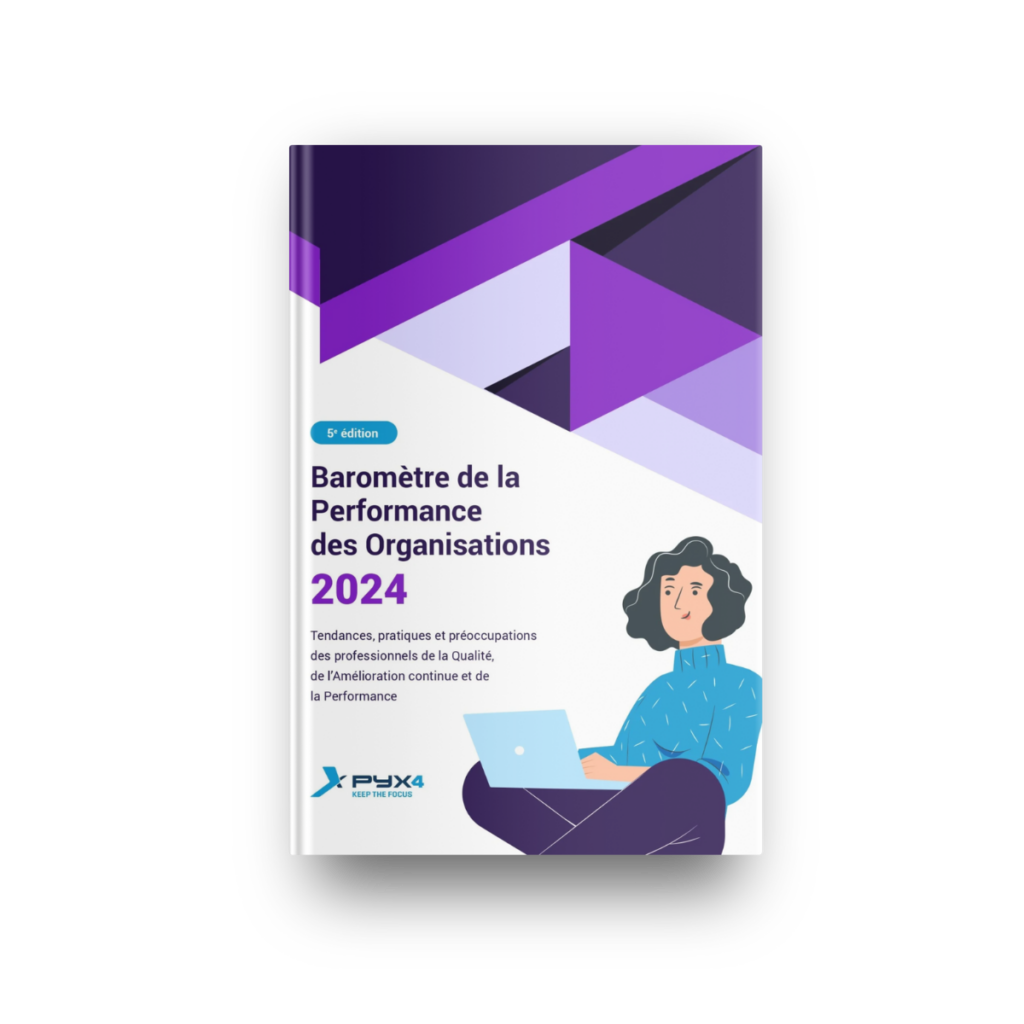
The IMS is part of a continuous improvement approach and can help meet these challenges.
Definition of an IMS, or QSE management
The integrated management system refers to the integration of QSE systems. It includes quality, environmental and occupational health and safety management, based respectively on ISO 9001, 14001 and OHSAS 18001 standards. It can also integrate other management systems such as energy (ISO 50001) and anti-corruption (ISO 37001). These ISO standards ensure the effectiveness of an IMS and should be considered carefully.
Some organizations include ethics and sustainable development concepts. In its most mature version, the finance and human resources departments are also included.
This management system integrates the operating methods common to each category that make it up without affecting their specificities. Currently, the IMS does not have its own reference system, which is why it is necessary to rely on the various Quality, Safety and Environment reference systems (and possibly on sustainable development and social ethics).
The Integrated Management System is part of a quality approach that aims to improve the company’s overall continuous performance.
Why implement a quality management system?
There are several reasons why implementing an integrated management system can benefit a company. Here is a non-exhaustive list of the benefits of an IMS:
- Analysis and reduction of the risks of inconsistencies in the company’s management.
- Optimization of resources through pooling
- Consistency of decisions and actions thanks to a global vision
- Productivity gains through the federation of activities in a unified management system
- Control through indicators
- Management of corrective and preventive actions
In summary, this approach aims to centralize and improve the management of all the company’s management systems. Adopting this approach will make the organization’s operations more efficient and much less costly.
What are the challenges of the Integrated Management System?
The main objective of the IMS is to integrate all areas governed by management systems into a single organization. This has a significant impact by simplifying work and avoiding conflicts and duplication of documents.
The IMS responds to the need to control the risks and performance of the company. Through this approach, the company can determine the risks related to its organization by analyzing all of its processes. The centralization of management systems allows managers to identify non-performing processes and activities that have little added value to the company’s overall performance.
Finally, the principle is to imagine solutions for continuous improvement and frequent controls to verify the achievement of the objectives set by the standards and principles decreed.
What are the challenges in implementing an IMS?
Deploying an integrating planning system can be extremely time-consuming and difficult. Several factors can influence the slowness of its implementation. The main factor is the cumbersome and complex centralization of processes that slows down the approach. Other issues such as the lack of expertise, the workload, the ability to work in a team and the management of the processes can also be observed.
The duration of implementing an integrated management system varies according to several variants. Does it depend, for example, on whether or not the objectives have been achieved (obtaining certification)? Is the budget allocated to the IMS sufficient? All these elements can affect the quality and the timeframe of the deployment of this quality approach.
How to implement a QSE approach?
Prior to the implementation of the SMI, all employees must be briefed and prepared so that they understand the approach and their involvement.
Step 1: the initial QSE audit of the company. This diagnosis is simply an assessment of the company’s current situation, the quality of its processes, its strengths and weaknesses, and the evaluation of its risks.
Step 2: Setting up the project management team. The management must get together to choose who will pilot this approach. Also, the allocated resources must be discussed and predefined.
Step 3: Project planning. What actions will be taken? What resources are needed (training and awareness of employees)?
Step 4: Define the operation. What are the responsibilities of each person? The implementation of a documentation system is essential at this stage of the deployment.
Step 5: Check and correct. What is the status of the project? You can set up a monitoring system that allows you to follow the process more closely.
Call a professional to help you!
As previously mentioned, the lack of expertise within the company can slow down the implementation of the IMS. It is indeed a complex exercise, and the help of an external experts in the field can be very beneficial. Beyond a fresh look, professional teams can bring you all the expertise that such a project requires. Pyx4 helps you implement an integrated management system by effectively targeting the risks and opportunities of your company!
The IMS is a strategic quality approach that every company should consider. It allows to be aware of the gaps in the different management systems and to solve the environmental hazards by centralizing these systems. Carrying out this project will enable you to make all your activities efficient and thus achieve customer satisfaction.