Lorsque l’on parle d’optimisation de la performance des entreprises, on entend souvent parler de la méthodologie appelée « Lean Six Sigma ». Mais qu’est-ce qui se cache exactement derrière ce nom aux consonances barbares ?
Il s’agit en fait de la combinaison de deux méthodologies complémentaires d’amélioration continue : le « Lean Management » et le « Six Sigma ».
Les principes du Lean management existent depuis toujours, il s’agit en effet de l’ensemble des bonnes pratiques permettant d’optimiser les activités tout en limitant les gaspillages.
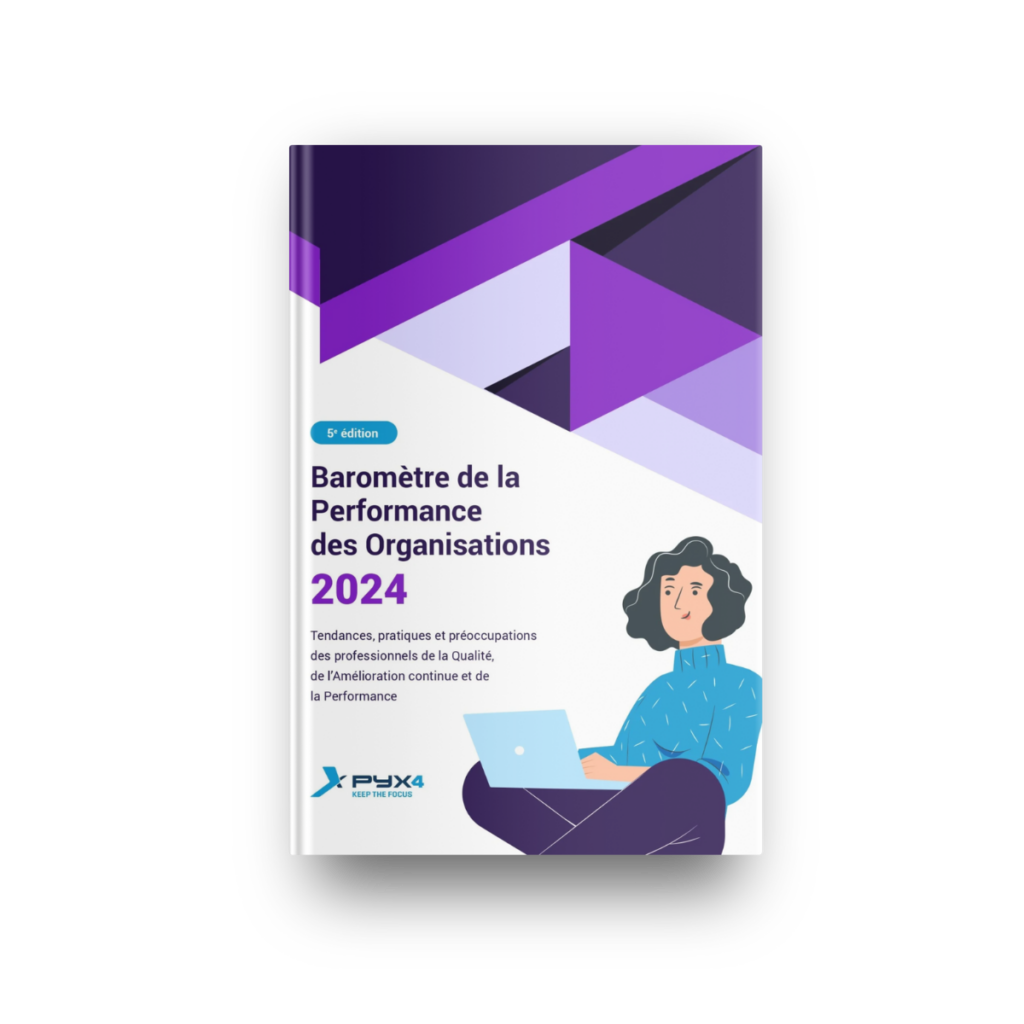
On dit par exemple que dès le 15ème siècle les Vénitiens organisaient la fabrication de bateaux en flux continu et lissaient leur production allant ainsi jusqu’à produire un bateau par jour.
La méthodologie « Lean » en tant que telle a été développée dans les années 1950 au sein du groupe Toyota au Japon. Elle s’est ensuite généralisée au le reste du monde, et notamment aux Etats Unis, dans les années 1980-1990. Les entreprises cherchant à s’améliorer appliquent souvent des principes de la méthodologie du lean management sans même le savoir.
La démarche « six sigma » quant à elle, est plus récente. Elle a été développée dans les années 1980, notamment par Motorola puis par General Electric.
Cette démarche cherche à annuler les défauts de production étape par étape en les ciblant systématiquement. C’est une méthodologie plus statistique et moins intuitive qui s’appuie sur le calcul d’un indicateur de performance : le sigma ou l’écart type. L’entreprise qui atteint la note de performance de « 6 sigma » a 99.9997% de succès dans sa production soit moins de 0.0003% de défaut.
Mais pourquoi parle-t-on alors de « lean six sigma » ?
Tout simplement car, bien que différentes, les deux méthodologies s’avèrent complémentaires et très intéressantes à utiliser ensemble. En synthèse : pour qu’un processus soit performant il faut qu’il soit efficace et stable.
Le lean management cherche principalement à rendre le processus efficace alors que le six sigma cherche principalement à rendre le processus stable (peu de variabilité). En alliant les deux approches, une entreprise maximise donc ses chances d’être performante.
Voici un tableau explicatif du « Lean six sigma », regroupant 2 méthodologies complémentaires, le Lean management et la démarche Six sigma :
A qui s’adresse le « Lean Six Sigma » ?
Le « lean six sigma » en tant que tel est aujourd’hui principalement utilisé dans les pays développés et dans les entreprises industrielles avec des productions en chaîne où un très haut niveau de performance est attendu.
Son application est par exemple presque systématique dans l’industrie automobile ou pharmaceutique. Pourtant, à des niveaux simplifiés, le « lean six sigma » peut grandement optimiser la performance de tous types d’entreprises et notamment des entreprises de services.
En fait, la question n’est pas de savoir à quel type d’entreprise le « lean six sigma » s’adresse, mais plutôt à quel type de processus.
En effet, pour qu’un projet de lean six sigma soit pertinent, il faut qu’il traite un processus auquel on peut associer un indicateur et un objectif, et autour duquel aucune piste d’amélioration spontanée n’apparait. Quand nous parlons de processus il s’agit bien d’une suite d’activités transformant une donnée d’entrée en une donnée de sortie en y apportant une valeur ajoutée.
Quelques exemples de projets « Lean Six Sigma » :
- Optimisation du processus de facturation fournisseur d’un établissement de santé privé
- Stabilisation de la satisfaction client selon les types de revendeurs d’un logiciel informatique
- Optimisation du stock disponible en boutique
- Etc.
Comment se déroule un projet de « Lean Six Sigma » ?
Un projet « Lean Six Sigma » suit les étapes appelées D.M.A.I.C = Define, Measure, Analyze, Improve, Control (Définir, Mesurer, Analyser, Améliorer, Contrôler). Considérons les grands principes de chacune de ces étapes :
ÉTAPE 1 du projet : Définir
Il s’agit de la phase classique de cadrage du projet, avec des travaux de préparation et de synthèse / compréhension. Lors de cette phase, Il convient de formaliser la problématique adressée, identifier les parties prenantes, constituer l’équipe projet, prévoir le planning, etc.
La modélisation du macro processus étudié est un livrable important de cette phase. Elle permettra de de clarifier l’ensemble de ses interfaces et étapes clés et sera le point de départ de l’ensemble de l’analyse. Une des principales difficultés de cette étape est de trouver le bon niveau de granularité du macro processus, qui deviendra en quelque sorte une carte des étapes de l’analyse.
ÉTAPE 2 du projet : Mesurer
La phase de mesure est très importante, car elle constitue l’étape de recueil des données.C’est également la plus fastidieuse et elle peut requérir un temps important si les outils consacrés à la collecte des données (souvent appelé business intelligence) n’existent pas dans l’entreprise. Des outils de résolution de problèmes (classiquement la matrice 6M* ie Ishikawa, ou l’analyse des risques AMDEC**) sont utilisés pour identifier les causes potentielles du problème, les classer et les prioriser.
Une cartographie des procédures plus détaillée peut-être utile lors de cette phase. Selon les besoins, on peut rentrer dans un grand niveau de détail d’analyse statistiques avec la sélection d’un échantillon représentatif et l’utilisation de lois statistiques (exemple : loi Normal, loi Poisson…).
ÉTAPE 3 du projet : Analyser
Une fois toutes les données en poche, l’objectif est alors de prioriser les points à analyser,en ciblant les causes ayant un impact significatif sur les défauts du processus. C’est la phase dite de « l’entonnoir » qui permet de ne retenir que les causes fondamentales. De nombreux outils statistiques sont désormais disponibles pour permettre de calculer l’impact de chaque critère sur la variabilité. Les causes entraînant le plus de variabilité seront traitées en priorité.
ÉTAPE 4 du projet : Améliorer
A ce stade, plusieurs méthodes existent pour réduire la variabilité des causes fondamentales identifiées. Celles-ci sont à adapter en fonction du niveau de maturité de l’entreprise afin de ne pas se perdre en détails. Il est par exemple possible, notamment dans les grandes entreprises industrielles, de réaliser un plan d’expérience. Il consiste à tester une évolution du processus sur un échantillon, afin de s’assurer de son impact avant de l’appliquer à grande échelle.
ÉTAPE 5 du projet : Contrôler
Une fois que le nouveau processus visant à limiter au maximum les défauts est mis en œuvre, l’objectif est de le faire vivre dans la durée. C’est alors qu’interviennent un grand nombre d’outils du lean management comme le 5S, le management visue, etc.
A travers ces différentes étapes, les méthodes du lean six sigma aident ainsi les entreprises à mettre en œuvre des axes d’amélioration de la performance.
Cette méthodologie qui a révolutionné le monde de l’entreprise depuis les années 80 continue aujourd’hui encore à avoir une portée significative.
*Matrice 6M : Matrice de priorisation des causes, régulièrement support de brainstorming. Les 6 M sont : Méthode, Matière, Milieu, Machine, Main d’œuvre, Mesure
** AMDEC : Analyse des Modes de Défaillances, de leurs effets et de leur criticité. Outil d’analyse des risques consistant à coter les risques potentiels d’une entreprise